Should employees be paid for non-productive time in the workplace? This is a very simple question, and the answer should surely be no.
Doing a bit of research brings to light a different picture though.
Being able to verify productive time is a crucial part in any manufacturing environment, yet it is overlooked so easily.
Let’s have a look at a scenario: Employee X arrives at work at 07:35 but does not immediately start with the job that was allocated to him. He first walks around, has a chat to a fellow worker and makes himself a cup of coffee.
Employee X then starts to work on the job at 07:50, takes a 37-minute lunch mid-day and completes the job at 16:15, before going home at 16:30.
In the short example above, 4 questions can be asked:
- How much time should’ve been allocated to the task?
- Was there a method in place to track time spent on the task?
- Was it cost effective?
- Was the employee productive for the eight and a half hours at work?
To solve these 4 problems, a system needed to be in place to provide the necessary feedback, which would improve productivity and costing during the manufacturing process.
Whether you have a small workshop or large manufacturing plant, there will always be a requirement to manage staff and tasks.
Uniclox has designed a system that will provide your business with the necessary components to track productivity during the manufacturing process.
Take control of productive time in the workplace. Contact us for a customised time and attendance solution that integrates directly with your payroll software.
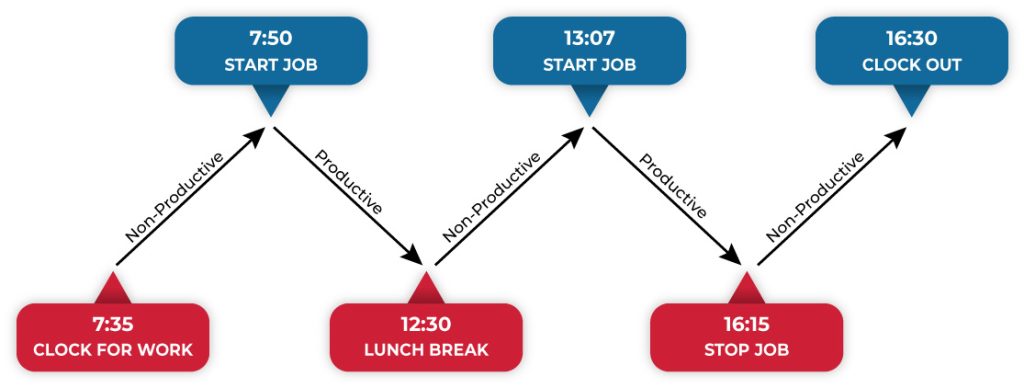